Demolition
Demo has revealed quite a bit and in any case, my project has increased in scope quite a bit. The general plan is the same but what is included is what has changed. I was unsure about the ceiling(gone), unsure about all the electrical (gone), unsure about the insulation (gone) unsure about plumbing (gone, everything except the stack and underground). The following are explanations.
A good reason why a lot of the switches don’t work is the wires either don’t go anywhere or go to J-boxes that are hidden and the connections inside are broken. What do I expect, the connections inside were taped together, not twisted, crimped or anything else. Found two more places where there had been a smoldering fire at some point around these hidden J boxes… holy cow.
Insulation: apart from the insulation in the accessible areas, which looked fine, everything else is done with 4 inch batt- Insulation value maybe R-5 or 6 since it’s old compacted and deteriorated.
The plumbing was a known issue, but how much was something else, I started to remove a branch waste line and everything attached to it fell apart. Also, I found out why the previous owner ran the water lines inside below the ceiling line. He had run the waterlines outside in the eaves and had covered them up with aluminum siding. The neighbor…other side neighbor told us that over the winter, the pipes had burst and sprayed water everywhere.
I’m on my 5th dumpster, this has been the regular site for the last while, I just wonder when I can say enough and end demo.
Cut the concrete for the new drain lines for the utility room and laundry room, Cut the concrete for the gas line to the range, cut the new window openings, the new door to the garage, the new door from the garage, the fireplace details, and for good measure the driveway.
Everything went pretty smoothly. The saw cut through the concrete well enough. The windows and doors were a pain because the saw was about 30 lbs, then add a hose attached with water spraying everywhere and the gyroscopic action from the blade spinning. I wet cut one side, then dry cut the other.
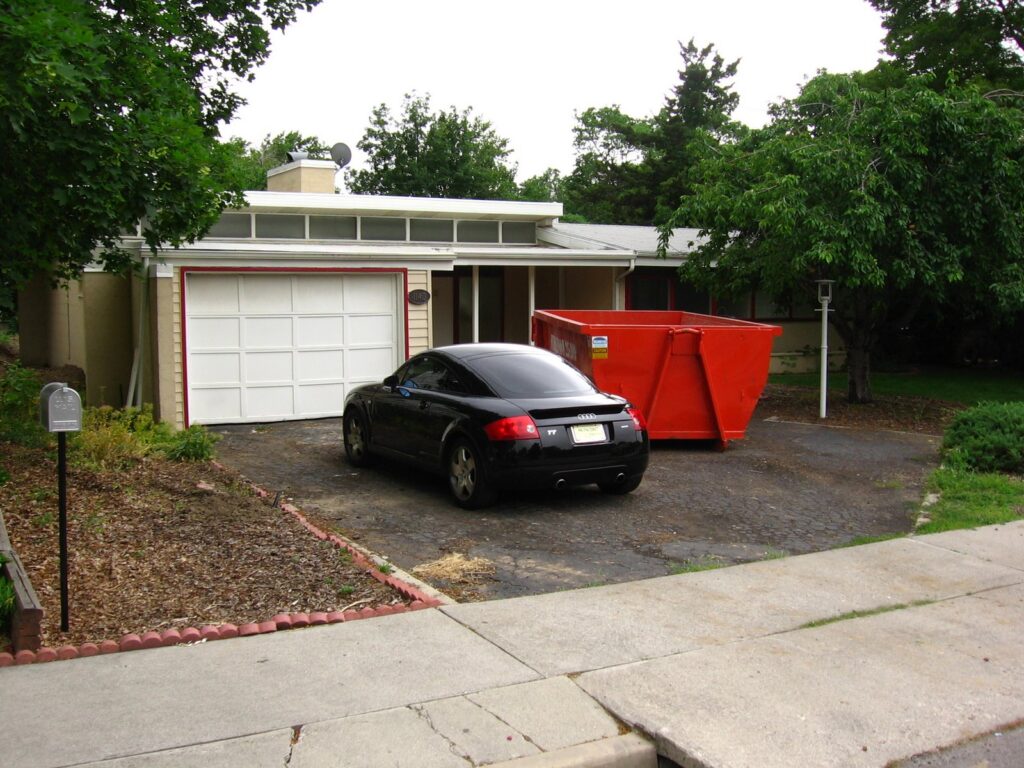
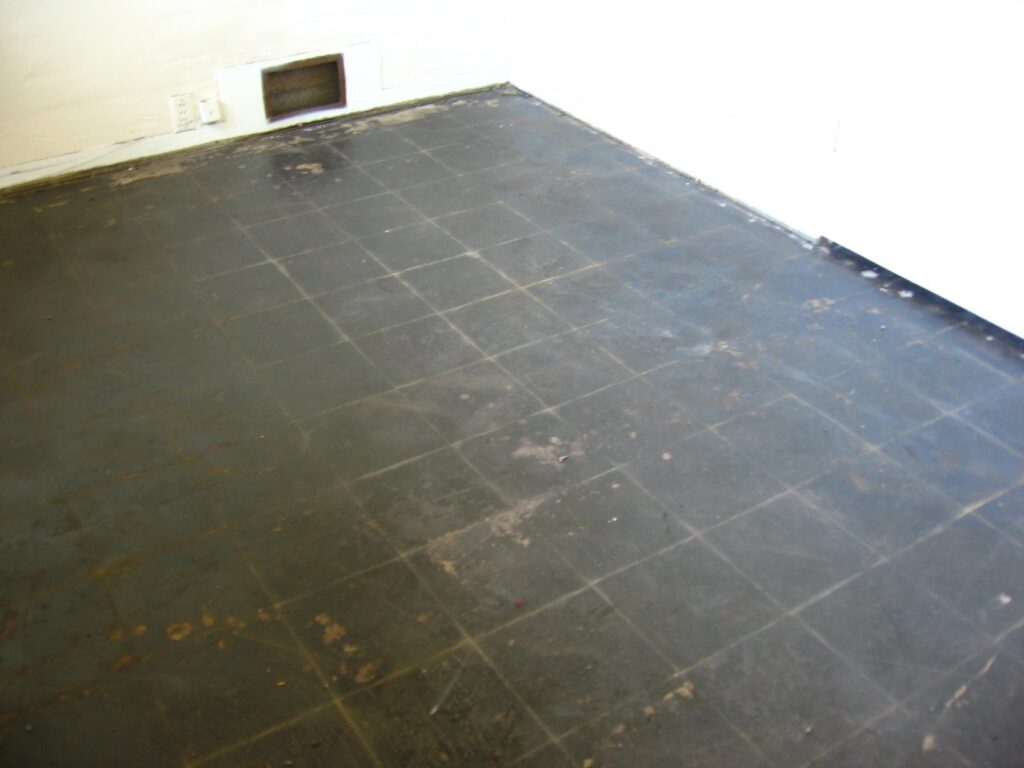
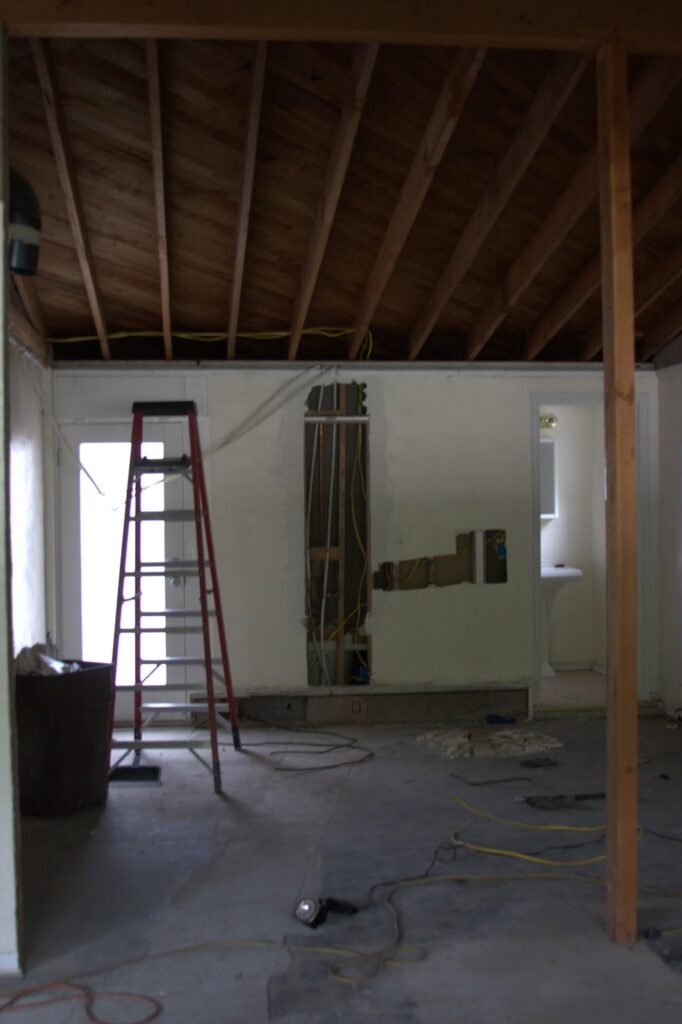